热门搜索
- 奥迪品牌
您使用 "" 找到了 条结果
热门搜索
- 奥迪品牌
您使用 "" 找到了 条结果
我们使用 Cookie 技术,以使得我们的网站可以更高效地运作,并给您带来更好的用户体验。目前我们使用 Adobe 分析工具 (Adobe Analytics Tool) 分析我们网站的访问情况,更多关于 Adobe 分析工具以及我们处理个人信息的内容请见我们的隐私保护声明。我们将在获得您的授权同意后启用相关 Cookie。
隐私保护声明
奥迪(中国)企业管理有限公司(“我们”)非常尊重您的隐私,我们承诺将遵照中华人民共和国个人信息保护相关法律规定来处理您的个人信息,就相应处理活动获得您的授权同意,保障您的个人信息安全并且确保您行使相关的权利。本隐私保护声明将介绍我们如何通过本网站收集使用您的个人信息。您阅读本隐私保护声明后继续浏览本网站的,表示您已完全理解并接受本隐私保护声明的全部条款和内容。
目前,本网站仅在获得您的同意之后收集并匿名化处理您的 IP 地址,我们不会收集使用您的其它类型的个人信息。若未来该情况发生改变,我们会在公布本隐私保护声明的页面向您详细阐述我们届时收集使用您个人信息的目的、方式与范围,并重新获得您的授权同意。若本网站就特定产品、服务公布单独的隐私政策,也请您仔细阅读并理解。
Cookies
Cookies 是包含数据的小文本文件。Cookies 存储于您的电脑硬盘中且不会造成任何损坏。网页中的 Cookies 不会包含任何有关您的个人信息。Cookies 的其中一个功能是可以在访客重复访问本网站时对其进行识别,这一功能是通过存储访客浏览器的随机识别符而实现的。
Cookies 能防止您再次填入相同信息,使特定内容的传输更加便利,并且帮助我们识别网上服务中尤为受欢迎的部分,从而我们将会使网页完全适合您的要求。
如果您想停用 Cookies,您可以随时在浏览器中更改并设置。请您使用互联网浏览器的帮助功能来了解如何更改这些设置。
目前,我们使用 Adobe 提供的分析工具( Adobe Analytics Tool )来分析本网站访问情况。Adobe 分析工具需收集您的IP地址,以分析您所在的地区。为完成前述分析,我们需将您的 IP 地址传输至位于中国境外的服务器(新加坡或者英国伦敦)。我们将在分析完成后针对您的 IP 地址进行匿名化处理。此外,我们将针对您的浏览器随机生成识别符,以分析您每一次访问我们网站的情况。我们不能也不会通过该随机识别符识别您的身份。我们基于使用 Adobe 分析工具而存储的信息不涉及您的个人信息。我们将仅在获得您的授权同意之后启用 Adobe 分析工具。对于我们委托处理您IP地址的公司,我们会通过与其签署协议的方式要求他们按照本隐私保护声明及我们的指示来处理个人信息,以保障您的个人信息安全。
第三方网站
本网站包含跳转至非我们运营的第三方网站的链接。我们不对此类第三方网站的内容负责,我们也无法控制此类第三方网站收集使用您的个人信息的行为。我们建议您查看您访问的每个网站的隐私政策,了解第三方网站运营者如何收集使用您的个人信息。希望您了解,前述第三方网站包括由我们关联公司运营的网站。
联系方式
如果您对本隐私保护声明存有任何疑问,需要进一步解释,或对您的个人信息处理有任何问题、意见或建议,请联系:
奥迪(中国)企业管理有限公司
电话:0086-10-6531-3000
2024.03.28
• 新产线无缝集成到现有车身车间和装配线中
• 奥迪 Q6 e-tron 车型系列在英戈尔施塔特工厂的生产实现碳中和
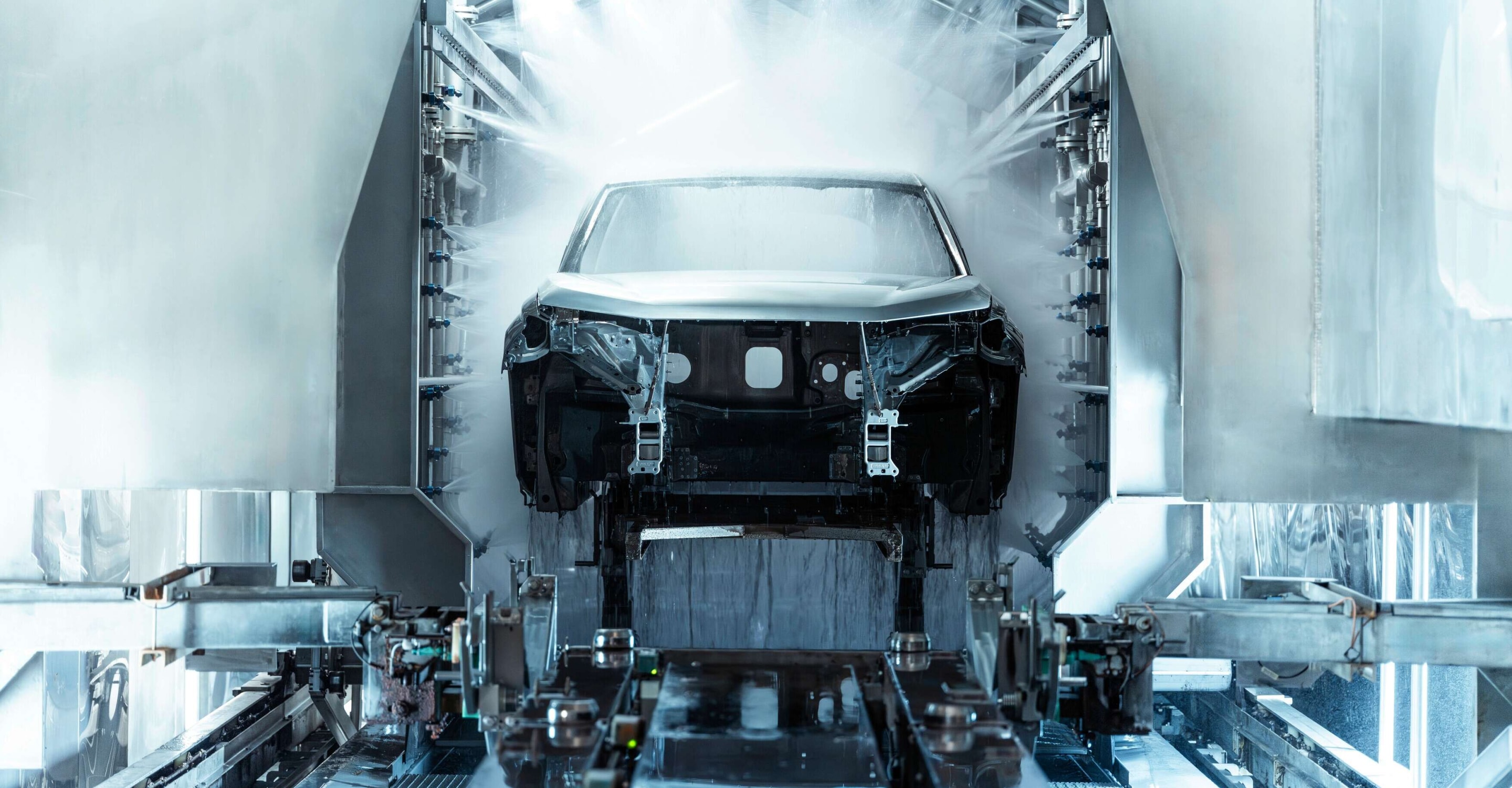
奥迪进一步提升英戈尔施塔特工厂奥迪Q6 e-tron喷漆车间自动化水平
自2024年1月1日起,奥迪英戈尔施塔特工厂成为继比利时布鲁塞尔工厂(2018年实现碳中和)、匈牙利杰尔工厂(2020年实现碳中和)后第三个实现碳中和 的工厂。此外,奥迪英戈尔施塔特工厂也是四环品牌在德国第一家设立自有电池装配车间的工厂。
奥迪全球 CEO 高德诺(Gernot Döllner)强调了首款基于 PPE 豪华纯电动平台打造的奥迪 Q6 e-tron 车型的重要性:“ PPE 平台和奥迪 Q6 e-tron 车型系列的投产为未来奥迪纯电车型阵容的发展奠定了基础。这是我们朝着目标迈出的决定性的一步:到2027年,奥迪计划在所有核心细分市场推出电动车型。” 奥迪汽车股份公司管理董事会生产及物流董事葛惟柯(Gerd Walker)表示,奥迪 Q6 e-tron 的正式投产是推进 “360工厂” 未来生产战略取得的里程碑式成就,“到2030年,奥迪在全球的自有生产基地都将投入电动车生产。我们正借助电动化的契机,推动奥迪工厂的全面转型。随着奥迪 Q6 e-tron 车型系列的顺利投产,
奥迪英戈尔施塔特工厂向着成为 ‘360工厂’ 阔步前行。” 面向未来生产,奥迪有着清晰的愿景。
在全方位助力可持续发展的 “360工厂” 未来生产战略的指引下,奥迪正推动自有生产基地的现代化和数字化转型。自2024年起,奥迪英戈尔施塔特工厂已成功完成转型,实现对奥迪 Q6 e-tron 车型系列及其它所有车型的碳中和生产。
这些电池将首先应用在奥迪 Q6 e-tron 车型系列中。与此同时,四环品牌正在为未来自主生产电池模块积累宝贵经验。奥迪英戈尔施塔特工厂的员工们通过汲取布鲁塞尔工厂生产奥迪 Q8 e-tron 的经验和盖默斯海姆电池测试中心提供的专业知识,受益良多。“通过这种方式,我们在扩大生产范围的同时也为工厂引入了新的生产技术。” 奥迪汽车股份公司管理董事会生产及物流董事葛惟柯解释道。
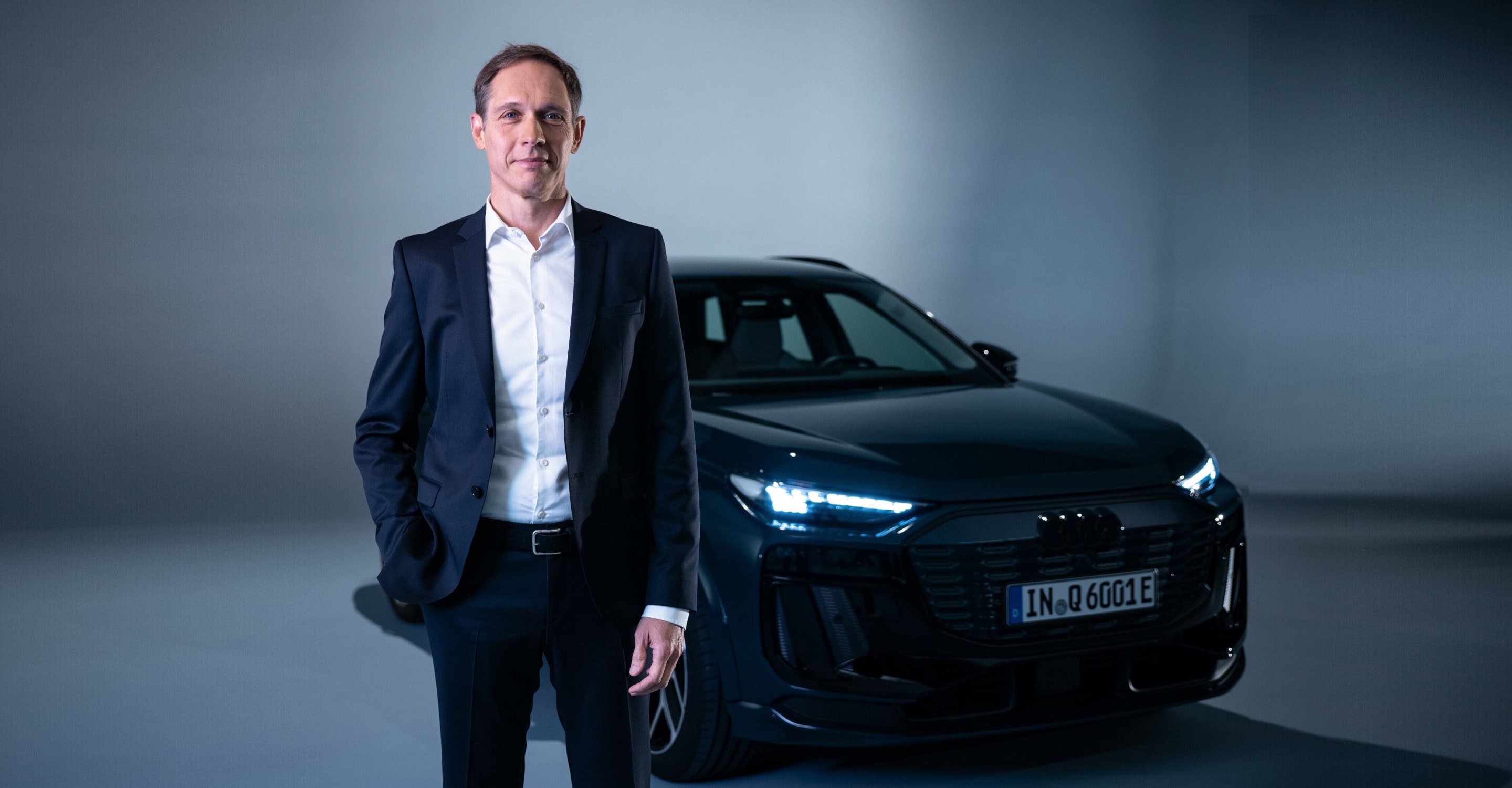
奥迪汽车股份公司管理董事会生产及物流董事葛惟柯
奥迪 Q6 e-tron 车型系列的车身部件由每班328名员工和1,150台机器人制造,自动化率达到87%。
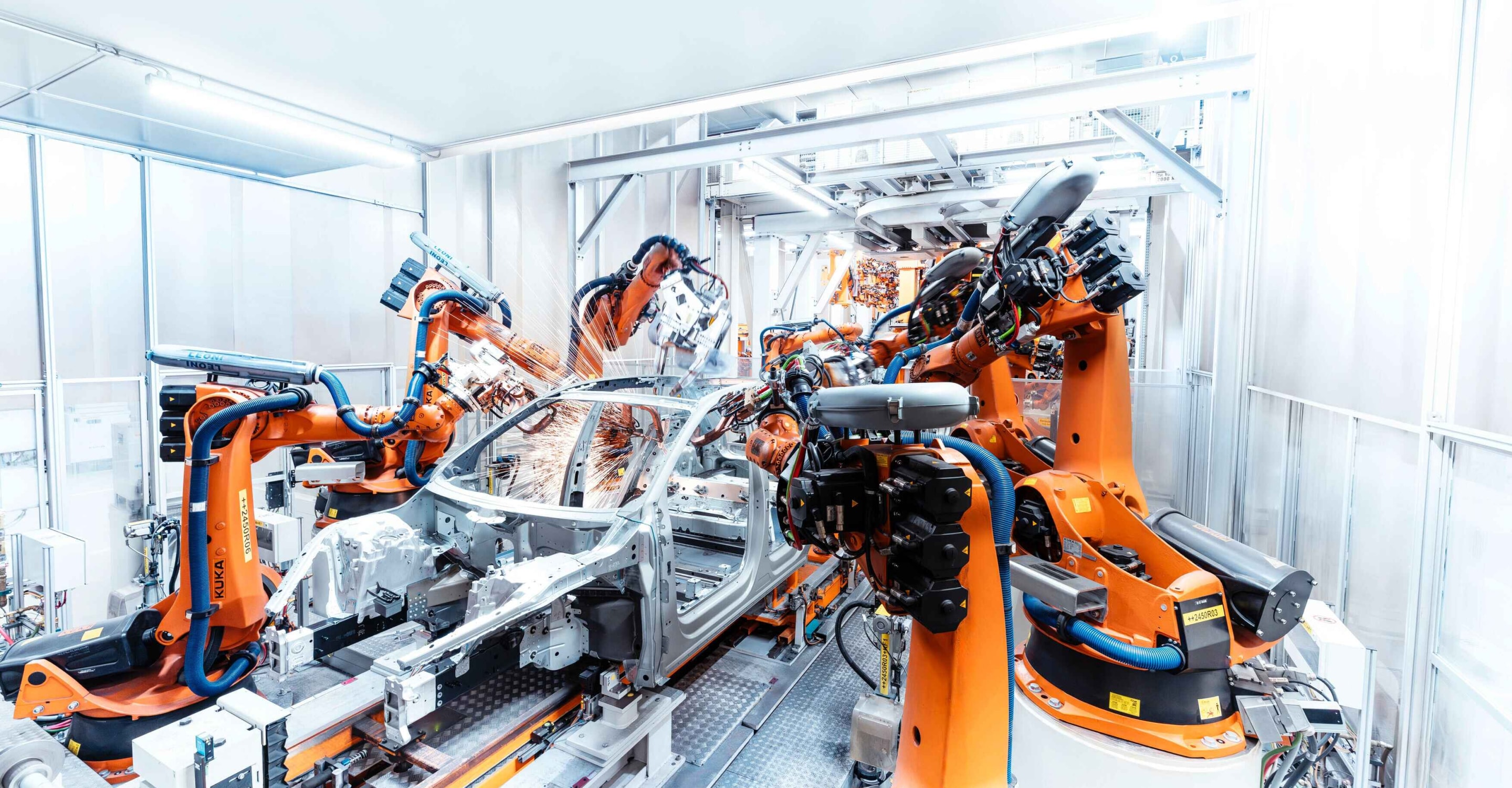
车身车间的自动化率达到87%
奥迪 A5 车型的装配线中。这样,不同车型系列的燃油车和电动车可以在一条装配线上完成组装工作。
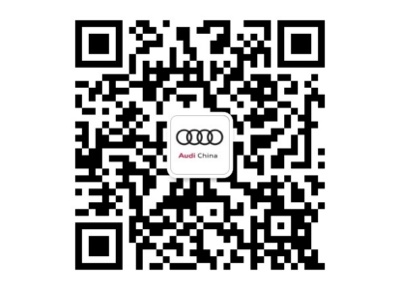